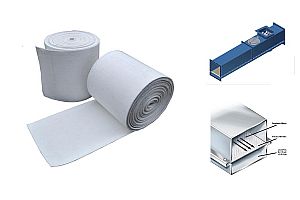
Introduction
Airslide technology is widely used in industrial operations to convey dry and powdery materials over short and long distances with minimal wear and tear. One key factor that concerns operators, designers, and engineers is the amount of energy required to run the system efficiently. This article explores the energy requirements for airslide technology, including key factors that influence energy consumption, and ways to optimize the system for energy efficiency.
Factors affecting energy consumption
The energy required to run an airslide system is influenced by several factors, including the type of material being conveyed, the distance, the flow rate, and the required pressure. In general, materials with high specific gravity require more energy to move than those with low specific gravity. Similarly, a longer distance between the inlet and outlet points requires more energy than a shorter distance. It is important to note that the pressure required to move a material depends on several factors, such as the angle of inclination, the type of fluidizing medium used, and the wall roughness of the airslide ducts.
Optimizing system design for energy efficiency
To optimize an airslide system for energy efficiency, it is essential to consider several design factors, including proper sizing of the compressor, minimizing pressure drop, and reducing the conveying distance. A well-designed air compressor will consume less energy while maintaining the required pressure and flow rate. Reducing pressure drop by minimizing bends, using a larger diameter pipe, and using low-friction materials can also help to decrease energy consumption.
Table 1: Comparison of airslide-specific power requirements
To better understand the energy requirements for airslide technology, it is useful to compare the specific power requirements of airslide technology to other conveying systems. Table 1 illustrates the specific power requirements for common conveying systems such as pneumatic, belt, and screw conveyors, as well as airslide technology. Specific power is defined as the power required per unit of material flow rate (kW/tonne/hour).
Conveying system | Specific power (kW/tonne/hour) |
Pneumatic | 30-120 |
Belt | 0.3-1.5 |
Screw | 1-10 |
Airslide | 0.03-0.1 |
Table 1 shows that airslide technology typically has a lower specific power requirement compared to other conveying systems. This low power requirement is due to the nature of the airslide system, which relies on the fluidization of the material to convey it through the system. This makes airslide technology a popular choice for conveying powdery materials over long distances while maintaining energy efficiency.
Maximizing energy efficiency (H3)
To maximize energy efficiency, operators must consider several strategies. Firstly, selecting the appropriate type and size of compressor that matches the system’s demand can help to reduce energy consumption. Secondly, maintaining the airslide system and addressing any leaks to prevent pressure drop can lead to significant energy savings. Finally, reducing conveying distance and optimizing layout can also help to minimize energy consumption.
List 1: Tips for maximizing energy efficiency in an airslide system (H4)
Choose an appropriately sized compressor that matches the system demand
Conduct regular system maintenance to address any leaks or blockages that may lead to pressure drop
Minimize conveying distance and optimize the system layout to reduce energy consumption
Design the system to reduce friction and pressure drop
Conclusion
In summary, airslide technology is an efficient conveying system that typically has lower specific power requirements than other conveying systems. However, to maximize its energy efficiency, operators must consider several factors, including type of material being conveyed, distance, flow rate, and pressure. Optimizing system design and layout, selecting the appropriate type and size of compressor, and minimizing pressure drop can help to minimize energy consumption and reduce operating costs. By implementing these strategies and maintaining the system regularly, operators can ensure that their airslide system is running at its peak efficiency, reducing their carbon footprint while maintaining output.